Press Brake Punch and Die require heat treatment. Moreover, heat treatment may have some defects.
How to prevent these problems? Today, Wuxi Shearchy professional metal forming machine supplier will do some analysis for you.
Bending Molds Manufacturing Process Analysis
CNC press brake punch and die heat treatment problems and solutions
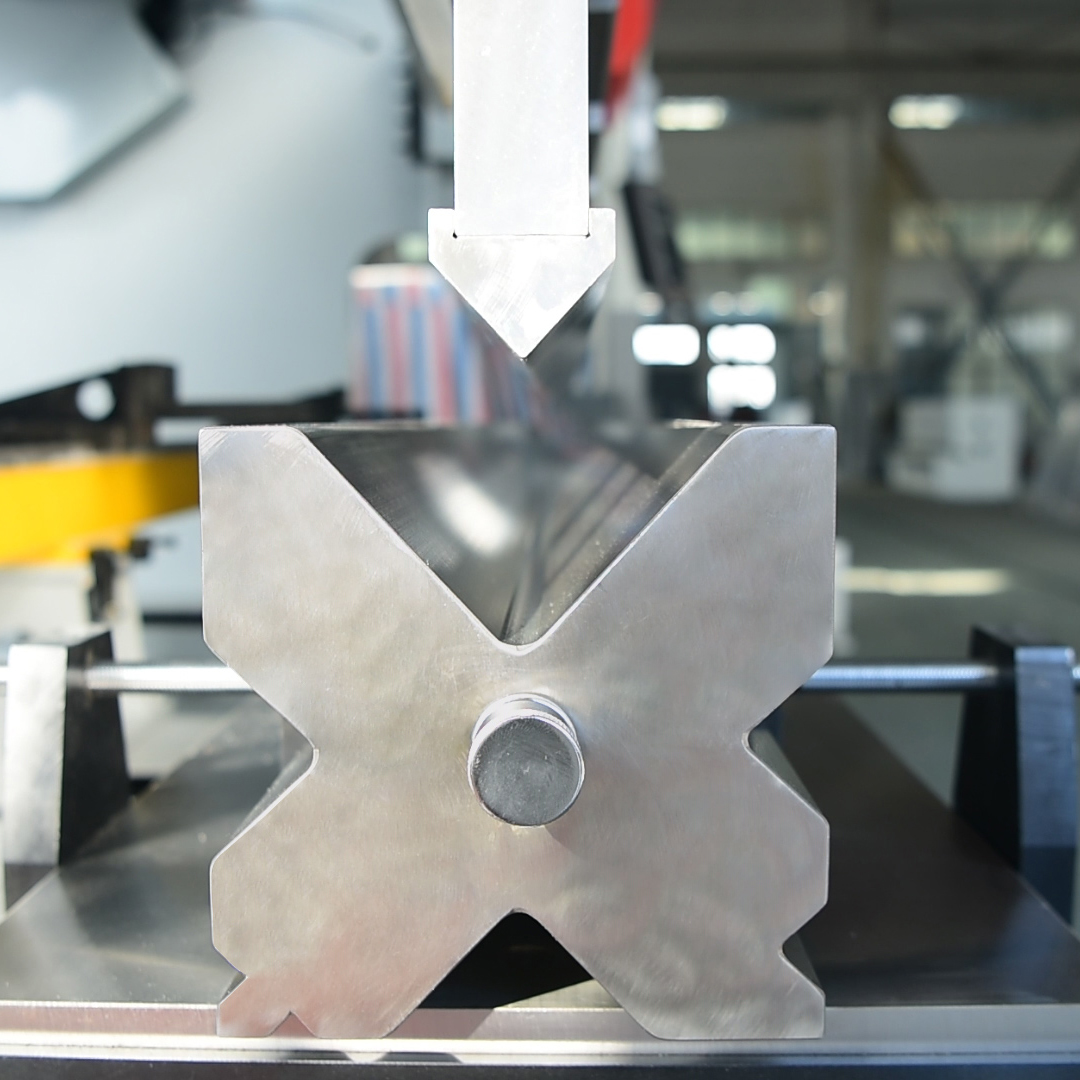
Problem 1: Soft point on the mold surface
Harm:
Bending molds after heat treatment has soft spots. Therefore, it will affect the wear resistance and reduce the using life of punches and dies.
Causes:
- Before heat treatment, the mold surface has oxidation, rust spots partial decarburization.
- After quenching heating, the cooling quenching medium is not selected properly. Or, the quenching medium has too many impurities or aging.
Solutions:
- Before heat treatment, we remove the oxidized and rusty parts of the mold surface. When quenching, properly protect the mold surface.
- Select the appropriate mold quenching cooling medium. For long-term use of cooling media, we often filter or replace regularly.
Problem 2: Structure poor before heat treatment
Harm:
So it will cause the die to be easily cracked and scrapped after quenching.
Causes:
- There is serious carbide segregation in the structure of press brake punch and die original steel.
- Poor forging process: too high heating temperature; too small deformation; too slow cooling after forging and so on. What’s more, all these will cause defects in the internal structure of the steel.
- Poor annealing process: too high or too low annealing temperature; too short isothermal annealing time and so on. And then, these will result in uneven or poor ball annealing organizational structure.
Solutions:
- Professional bending machine mold manufacturer will choose good quality tool steel materials according to the working conditions, production volume and material strength and toughness.
- Improve forging process or adopt normalizing heat treatment.
- For high carbon die steels with serious carbide segregation not be forged, we adopt the solid solution refining heat treatment.
- Reasonable installed furnace to ensure the uniformity of inner mold temperature.
Problem 3: Press brake bending mold quenching cracks
Harm:
It is the biggest defect in heat treatment. Further, it will directly lead to the scrapping of finished Press Brake punch and die, resulting in serious economic and production losses.
Causes:
- Firstly, serious carbide segregation in mold material.
- There is mechanical or cold plastic deformation stress in the molds.
- Improper operation of bending tools heat treatment.
- Molds are complex in shape, uneven in thickness, with sharp corners or threaded holes that cause thermal stress and tissue stress too large.
- Also, die quenching process is improper.
Solutions:
- Strictly control the internal raw materials quality of bending machine punches.
- Improve forging and quenching process.
- For the mold after mechanical processing or cold-plastic deformation, first de-stress annealing, and then heating & quenching.
- Take the right grinding process as well.
WUXI SHEARCHY Technology supplies a large range of punches, V-dies, adaptors and clamps to suit most types of Press Brake machines. Tooling is available to suit all mounting tangs. As well as standard tools, specials can be manufactured. If you are in need of bending punches or dies, please contact us at once!